Tapered Reamers
Tapered Reamers
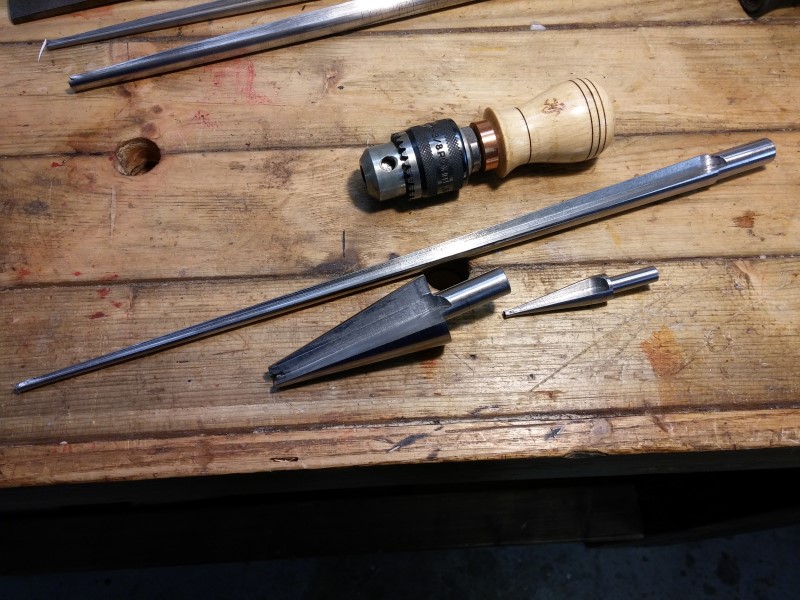
Table of contents :
Tapered reamers
In the field of woodwind instrument making, one thing is particularly
challenging for many amateur luthiers, I want to talk about the bore.
The bore is the inner part of the instrument, it will determine the acoustic
characteristics of the instrument.
Boring the instrument therefore represents a difficult challenge for the
amateur and this requires a certain amount of know-how and tooling.
In wind instruments, we can distinguish two big families:
-
The flutes.
The bore is approximately cylindrical, slightly tapered actually on the flutes, for a question of compensation of the higher octave which would otherwise be a little too flat. -
Reed instruments.
The reed instruments are still divided into two sub-families which are:
- The Clarinet family, with cylindrical bore and simple reeds.
The cylindrical bore is simpler to achieve, but these instruments have, because of this cylindrical bore, a particular characteristic, which is they do not produce the octave with the same fingering. By changing the register (by blowing harder), we get the octave + a fifth and not the simple octave like on flutes or oboes.
A cylindrical bore is made first by roughing out the hole using fairly
conventional tools (long drill bits, “D-bits” or “gun drills”).
See this other article dedicated to long holes
drilling.
The finish is achieved using a machine reamer, which are common tools that can
be found easily in any diameter.
- The oboe family, with tapered bore and double reed.
The slope of the cone is designed so that the instrument gets the upper octave, keeping the same fingering.
The tapered bore, however, is much more difficult to make, and this is what I
will develop here.
The bore is roughed out
using the same tools as mentioned above (gun-drills, D-bits), but only the
smaller diameter will go through from one end to the other.
The cone will be roughed out by a succession of cylindrical holes becoming
shorter and shorter as the diameter grows. (see the picture below)
Step drilling
The finished cone will be obtained using a tapered reamer.
It is this reamer that is the most important because it represents the
negative shape of the inner bore of the instrument.
These reamers are not standard at all and can not be commercially obtained.
Professional makers have these tools manufactured by professional toolmakers
but the occasional maker will have to make them himself.
Information about this crucial phase is not legion on the web or in the
literature, but searching carefully, we can still gather a certain amount of
information.
After a lot of attempts on my side, I’m happy to be able to share here two
variants of the manufacture of this tool. There are others of course.
Here I’m going to show how I make the tapered reamers with straight flutes.
As is often the case when making wind instruments, the metal lathe is
essential for this operation.
I offer two options for making the flute, milling, or grinding if you can not
access a milling machine.
For making a tapered reamer, there are three phases:
-
The machining of the cone on the metal lathe.
-
The machining of the flute.
I propose two methods :
-
A method by grinding
-
A second method, maybe more academic, but that requires access to a milling machine.
In both cases, we will see that it is necessary to make some additional tooling in order to immobilize the reamer, which can be very long and thin, during machining.
-
Honing and sharpening.
These are manual but essential operations.WARNING: It goes without saying that everything that is shown here needs to be already familiar with all these tools and metal machining in general.
The use of these machine tools is very dangerous for anyone not warned, and requires the application of strict security rules.
If you are not already experienced in these areas, I do not recommend you to undertake alone this project, get help from a machinist !
Making the cone
×
- 1 -
|
- 2 -
—|—
Let’s start with a bit of history … The ancient makers did not have the machine tools that we use today. Testimonies report that one of the favorite sources of elders to make their reamers was to re-use bladed weapons. Swords, bayonets … I myself have considered this option and I still have in my workshop a whole arsenal … (Sword and foil for fencing, World War II bayonet.) But to tell the truth, even if the steel is certainly very suitable, the dimensions did not seem usable for the moment.
|
Here is a reamer that belonged to the legendary luthier Jean-Pierre Jacob, the most famous maker of binious and bombards of the late nineteenth, early twentieth century in Brittany, France. It is certainly a bayonet of the Napoleonic era. The proximity of the arsenals of Brest and Lorient where some metal working took place also led to the use of long files, annealed and reshaped with a taper.
- 3 -
|
- 4 -
The adventure begins with the supply of tool steel. Personally, I do not practice heat treatment for my reamers. They only serve me at small scale, so wear is not really an issue in my case. By cons, I choose a steel that is already hard enough. The machining is a little more delicate, but the result is very correct. Here it is pre-treated 42CD04T steel, from www.blockenstock.com/
|
The work begins with the machining of a cylindrical shank that will be used to hold the reamer in the chuck. We see in the background the machining plan prepared in advance that will give me all the dimensions (intermediate diameters and intermediate lengths). For a simple cone, I prepare it using a spreadsheet, available here.
- 5 -
|
- 6 -
- Tracing. I scribe the intermediate lengths on the metal bar. A personal trick
- rather than individually measuring the different strokes, I make a drawing with my CAD software, which I print full scale, and then I scribe the marks on the metal.
|
Marking. Using a carbide tip in the tool holder, I trace on the lathe all the intermediate steps.
- 7 -
|
- 8 -
There are several ways to machine a taper on a lathe. But reamers for wind instruments are usually long and of very low slope. Machining between centers, with the tailstock offset-ed or using a taper attachment is simply unthinkable here. Moreover, for musical instruments,the bore is almost never a true cone. The reamer can have several sections of different slopes or a bell shape end and so we need to create custom profiles. It is for this reason that I use only stepped machining to rough out my reamers.
|
The machining plan gives me, on each step, the exact dimension to respect. By doing so, the tool always works very close to the mandrel, which avoids any vibration or chattering. Here I changed the cutting tool to take the finishing pass and turn the shoulder that must be precisely made, because the corner of the shoulder is the definitive diameter.
- 9 -
|
- 10 -
As you progress, you pull the tailstock back pull the workpiece from the chuck a little more. Care should be taken to always keep the same alignment of the jaws of the chuck, in order to guarantee as much as possible the concentricity of each step with the previous ones.
|
Need to be patient, you have to stay focused …
- 11 -
|
- 12 -
Here is the outline of the taper. The steps are distant by a diameter of about half a millimeter.
|
Finishing. The steps can be taken off by tilting the compound slide, but in the case of a very slight slope like here, I prefer to just work with a file. I spay the workpiece with marking blue, and I walk slowly and regularly the file, the lathe turning at moderate speed. Be careful not to remove all the blue!
- 13 -
|
- 14 -
We start with a bastard file, then a thin file, and I finish here with emery cloth of grains 80, 120, 240, 400 and finally steel wool.
|
And here is the cone finished and polished. All this operation must be done with great care and dimensions constantly checked against the machining plane.
Flute : Method 1 - grinding
- 1 -
|
- 2 -
—|—
First method to machine the flute. I am going to use an angle grinder, fixed
on a cross slide table. You can see the description of this homemade cross
slide table [ here](http://www.homemadetools.net/forum/cross-slides-grinder-
support-wooden-made-13624)
The cone of the reamer is fixed between centers, set at the correct height,
thanks to these vertical supports.
|
On one side, the shank of the reamer is fixed in a drill chuck, itself screwed on an extension rod. (reuse of another tool).
- 3 -
|
- 4 -
The chuck
|
On the other side a rudimentary dead center made of a screw and a nut.The screw is pointed and fits into the center hole of the reamer.
- 5 -
|
- 6 -
And here is the grinder installed so as to machine longitudinally. Watch the video of the fixture in action.
|
The cutting effort is directed along the axis of the reamer, there is no deformation or vibration.
- 7 -
|
I work outside because there are a lot of sparks …
| Grinding a reamer.
Method 2 - Milling
- 1 -
|
- 2 -
—|—
Another method, by milling. If you have a milling machine, this method is preferable because it is more accurate.The main difficulty for this milling job stands mainly in the immobilization of the piece. The reamer, in its thinnest part, has a diameter of less than 4mm … There are different solutions for this problem, but here is by far the most efficient one, which remains quite simple. This fixture appears in an article by John Hugues in “The Sean Reid Society Journal-Vol2”.
|
The basic idea of this fixture is to use some kind of small steady rests, drilled with holes of stepped diameters, and welded vertically on a base. If you have a large milling machine, these supports will be bolted directly onto the table of the machine, in a T-slot. In my case, I have a milling head on the bed of my lathe and my table is very narrow. In this case, I made a rail from a square tube, grooved in its length, which allows me to bolt the supports. The rail is fixed in the vice of the milling machine.
- 3 -
|
- 4 -
Each of the supports has an opening for the passage of the milling cutter, allowing access down to the axis of the reamer.
|
This set of supports, which can be bolted at any distance along the rail is very versatile and can fit any slope or length of reamer. In the foreground, we see the example of a short reamer that does not require any intermediate support. At the end, a split block with a clamping screw is used to fix the tail of the reamer, and on the other side, a pointed screw and two nuts serve as dead center. This screw is a throw out part, since it will be machined when the cutter will reach the end of the reamer.
- 5 -
|
- 6 -
The full setup, in action.
|
Milling
- 7 -
|
- 8 -
Milling
|
A large table of milling machine would be better, but for a reamer of about thirty centimeters, it works pretty well like so.
- 9 -
|
- 10 -
Case of a bell reamer, shorter.
|
Case of a very small reamer, for the reed seat.
Straight reamers
1/3
Case of a straight reamer.
2/3
It is easy with this method to make straight reamers
to non-standard diameters.
3/3
For straight reamers, several flutes can be made.
In this case I used a dovetail cutter.
❮ ❯
Honing / Sharpening
- 1 -
|
Honing. The last phase is to hone on a stone the surface of the flute. Here I use diamond stones of different grit.
—|—
- 2 -
|
The edge must be very clean along the entire length.
- 3 -
|
Sharpening. This step is essential for operating this type of reamer. A small burr along the cutting edge should be raised, this tool working as a cabinet scraper in fact. I rub all the way by pressing a tool called a burnisher, made of very hard steel.
- 4 -
|
Another way of doing it, here with a triangular section burnisher. The goal is to form a small hook-shaped burr outwards. It is this hook that will form the chip (see the operation of a cabinet scraper).
- 5 -
|
It’s a long and laborious job, but this method yields very good results.
- 6 -
|
The small reed seat reamer.
And here are a couple of videos showing how these reamers are used.
See also, more in details, the making of a conical bore
flute.
Do not hesitate to comment here below in case of any question or you can
contact me
also on my Facebook page.
Happy machining!
Christophe
Older readers comments
Hello from ThirdBike